超辐界二氧化碳液态染色研发趋势
1.传统染色的载色体(Vehicle)是水。水是宝贵的自然资源,尤其在中国。因此染色工作者把载色体从水换成临界二氧化碳液体进行染色、洗涤、整理作为节水的重点科研对象。
一、超临界二氧化碳(又称SCF-C02)液态染色的关键因素
1.1二氧化碳超I临界的必要条件
Hyatt论述到二氧化碳热力学性质时指出,其成为液态C02的超临界点,压力20Bar时,大约为31℃。液态高压范围为20~73Ba,且液态二氧化碳为疏水性的。
1.1.2两亲助剂的使用
虽然液态C02用于染色(包括洗涤、整理)。并不需要多相体系,但由于液态C02对疏水性染料.油、脂肪、类脂的溶解度属微溶状态,仅用 二氧化碳,得色率和效果并不好。因此需要助染的助剂。助染助剂最为适合的是一种既亲油,又亲水的两亲助剂。如液体溶剂、醇、碳氢化合物、醚、胺、酮及其混 合物。此外两亲聚合物是随机嵌段(二嵌、三嵌、多嵌或生成聚合物的嵌).接枝共聚,星型均聚、共聚低聚物等。
溶剂是指高沸点低蒸汽压得那种溶剂,闪点必须高于37.8℃、一般在60.5℃、而93.3℃或更高的更好。如石蜡及异构的混合物。
助溶剂包括醇:如乙醇、异丙醇、丁醇,辛醇、癸醇、十二醇、十六醇等C2----C16醇;卤化烃:包括氯三氟甲烷、三氯氟甲烷、过氟丙 烷、氯二氟甲烷、硫代氟乙烷等;胺(如N甲基吡咯烷酮)。酰胺(如二甲基乙酰胺)l酯(如醋酸乙酯、二元酯、乳酸酯);醚(如二乙醚、四氢呋喃、乙二醇 醚);脂肪族碳氢化合物(如甲烷、乙烷、丙烷、氨基丁烷、正戊烷、已烷);氧化物(氧化氮);烯烃(如乙烯、丙烯);天然碳氢化合物(如萜烯,双苎烯); 酮(丙酮.甲乙酮);烷基吡咯烷酮、硫代恶唑等。
聚合物:如聚甲基硅氧烷、聚(苯乙烯-g-二甲基硅氧烷)、聚(甲基丙烯酸-g-1,1’二氢过氟辛酸甲基丙烯酸酯)、聚(1,1’二氢 过氟辛酸-g-苯乙烯)等。(近年来美国认为过氟辛酸衍生物疑似致癌物)。由这些助溶剂与液态C02的复配将使分散染料疏水纤维(如锦纶、涤纶)的得色率 和递深性比单独C02液有很大的提高。
1.1.3用含湿蒸汽解决亲水性染料的染色问题
由于阴离子染料属于亲水性染料,它们并不溶解于疏水的液态二氧化碳之中,水基本上也很少溶解于液态的二氧化碳之中,一般溶于C02的水不 超过5%(重量/体积),而在液态时C02中含水仅为0.5%“1.0%(重量/体积)。当液态二氧化碳染色体系中引入了吸湿的纤维时,此体系用亲水染料 染亲水性天然纤维如羊毛、蚕丝、纤维素纤维及其与疏水性纤维的混纺变得可能。棉和丝所用纤维的含湿度在50~100%范围内,以75%含湿度为最适;而羊 毛和黏胶所用纤维的含湿度在60~100%范围内,以75%为最适。
1.1.4用胺化剂制“活性棉”
棉布即使吸湿了,染色还比黏胶的浅很多,因此在液态二氧化碳系统中染色,一般是需要用胺化剂对棉纤维引入氨、仲氨的共价键合基团,使棉成 为对阴离子染料增加染座的“活性棉”以起到增深效果。当棉布氨化处理后,纤维上含有叔胺或季铵盐的基团,棉及混纺织物通过水中含保温剂(保湿剂一般用三聚 氰胺、尿素、硫代二乙二醇等)。使之棉织物含有充分湿度就可染色。
1.1.5为改善色牢度染料引入活性基
用一般分散染料,以液态二氧化碳超临界点,发现色牢度还是不够好。于是在分散染料上引入活性基团、制成活性型分散染料,因此种染料对纤维素产生了共价键合,故色牢度显著提高。
1.1.6调节温度和SCF-C02密度以控制染料相分配用SCF-C02超临界染色,染料在SCF-C02相和被染的纤维相这两相中的分配有密切关系。
当温度维持不变,适当降低SCF-C02密度时.染料在C02液中的溶解度并没有显著下降。反之,当度下降,尤其是降到纤维Tg(玻璃转 化点)以下时,染料溶解度会显著降低。也即当SCF-C02跌至临界点之后,C02液吸收染料的速度是比纤维吸收染料的速度快,因此出现了染料沉淀和摩擦 牢度问题。为解决问题.染色过程设置了SCF-C02二个密度区。首先第一密度区,密度值较高,范围在0.4~0.7g/cm3,以0.62g/cm3为 适宜的值,温度在Tg点以上在染色温度下保温循环30~45分钟,液循环速度控制在27.8~45.4升/分钟。然后以0.0037--0373kg/分 钟的速率,降压进入第二密度区,密度控制在0.3~0.5g/cm3范围,以0.45g/cm3为适宜,温度控制恒定值。某些分散染料(如红167,黄 86,蓝60,紫9l等)在恒定温度下,有控制地降低SCF-C02密度,结果染料溶解度的降低不显著,这可认为溶解度在控制范围内。此时染料从SCF- C02液中被吸出是有利于纤维吸收的。
另一方面,如果维持密度(SCF-C02)不变,则降低温度,以密度控制使染料在SCF-C02中溶解度显著增加。随着降温,染科上染纤 维的速度慢于染料从C02液中析出的速度。导致染料沉淀及摩擦牢度问题这说明染料从溶液中向纤维上的分配情况错综复杂。它不仅依赖于染料在SCF-C02 中的溶解度,而且还依赖染料对纤维的亲和力。这一点在选染料时很重要。如分散蓝77号对涤纶(对苯二甲酸乙二醇酯)的亲和力很高,可以优选。
1.1.7染色载体的筛选
在SCF-C02 (即超临界二氧化碳)染色体系中,选用两亲的助溶剂可改善吸色率、固色率。然而对某些亲水纤维的深色染色仍有困难。此 时选择载体是必须的。载体的主要作用是降低纤维的玻璃转化点,提高染料在纤维上的分配比。为此,美国北卡罗琳娜大学以三氯苯用壬基苯酚聚氯乙烯醚为乳化剂 作载体染色试验,在天然纤维和合成纤维上染色基本是成功的。例子如下:
例1:棉纱筒子密度0.5g/c.c
以C.1直接兰78号.用量22%o.w.f
染色条件:SCF-C02液密度0.6g/c.c
温度/时间:40~83℃,流速31.822升/分钟-磅
液流循环1→0/5’ →O→I/5’
结果染得深兰:干摩4~5级,湿摩3~4级
例2:羊毛精纺纱(没经洗漂)
以C.1酸性红360号,用量5%o.w.f
SCF-C02液密度0.7g/c.c
温度80℃/30分;流速31.822升/分钟-磅
流向O→1内循环
结果染成深红色,干湿摩擦均为4.0级。
(按AATCC试验法8号) .
例3:尼龙6染色
以C.1酸性红360号;用量5%o.w.f
SCF-C02液密度0.65g/c.c
温度/时间:100℃/30分钟,流速31.822升/分钟-磅
流向0→1内循环
结果染成深红色,干/湿摩擦均为4.O级。
例4:腈Orlan75
用C.1阳离子兰28号,用量5%o.w.f
SCF-C02液密度0.65g/c.c
温度/时间:100℃/30分钟,流速31.822升/分钟-磅
流向O→1内循环
染得很深,干/湿摩擦均为5.O级。
例5:涤Dacron54、64、107W(杜邦)
涤纱筒子密度0.5g/c.c
染料用C.1分散兰56号,用量0.89%(糊状)
SCF-C02液密度0.6g/c.c
温度/时问:100℃/30分钟,流速68.19升/分钟-磅
流向1→0/5’,O→I/5’
染得深兰色,表观上摩擦牢度无问题。
例6:涤50/棉50混纺
纱筒子密度0.49/c.c
染料用C.1分散兰56号/C.1直接兰78号,用量2.22%.o.w.f
SCF-C02密度0.33g/c.C
温度/时间:lOO~C/30分钟,流速31.822升/分钟-磅
流向1~O/5’,0~I/5’
染得深兰色,相当于有3%o.w.f的染深性
干摩擦4~5级,湿摩擦4级。
1.1.8待研发的问题
①棉染色后强力下降 (553-68)/553=485/553=87.7%
②寻找绿色载体,三氯苯有毒!如NMMO等环保型助剂。
2羊毛和蚕丝的冷轧堆染色
上个世纪80年代为了节约能源,有人开发出冷轧堆工艺。
2.1低温冷轧堆染色工艺。最初用乙烯砜活性染料在偏酸性条件下将毛织物轧活性染料液,结果得色率很差。色牢度也不够好。后来赫司脱公司 得Richter改用弱碱性浴PH7.0 9.0之问轧染,得色效果不错,堆放时间是24小时,活性橙16#,浓度2%.润湿剂0.5%,碳酸氢钠2%, 轧液率95%,室温堆卷24小时,然后先用40℃水洗一次,再在80℃水槽中,PH8.5,洗15分钟,结果色牢度很好,这一工艺优点是尿素用量比传统的 300g/L低得多,只用100g/L,但要求羊毛染色前经过防缩或机可洗处理。句话说这种冷轧堆染色适用于防缩处理毛。
2.2国际羊毛局的Graham对冷轧堆工艺进一步作了改良,被冷轧堆得羊毛不必是防缩羊毛,所用染料从棉用活性染料进一步扩展到耐缩酸 性、酸性媒介、1:2金属络合和1:1金属络合染料。主要手段是在轧染染料之后,卷堆之前插入一道电射频处理,用的是20千瓦的电射频发生器频率为 27.12M Kertz和25千瓦的电射频发生器频率为13.5627.12 M Kertz。染色材料在轧液后于60℃条件下辐照15分钟,然后去堆 卷过夜至次日,在Fleisser4槽中,复洗机依次冷水/60℃/50℃/35℃洗涤后烘干。
轧堆举例如下:
20g/kg中性上青S-B11
100g/kg尿素
16g/kg异丙醇 ·
lg/kg醋酸
20g/kg Detergy1 EDC
3g/kg Etiggal S
结果水处理牢度为4/4/4
碱汗渍牢度为3-4/4/4
按ISO洗二次为4/4/3-4
2.3汽巴公司开发了活性染料冷轧堆染丝
轧堆例句如下:
610克活性染料(乙烯砜型)
lO克琥珀酸二辛酯钠盐
200克碳酸钠
120克海藻酸钠
加水至10升
织物为单位重量80克/米2丝绸110米,轧液率90%,于25~27℃卷堆48小时。然后用40~50℃沮水冲洗10分钟,再放于含 2g/L非离子洗涤剂的平幅洗机中80℃洗15分钟去除没固着的染料,然后用纯碱调PH8.5~9.0,40℃洗5分钟,再用20℃水洗5分钟(水中含 lg/L醋酸)染得深而均匀的颜色,湿牢度很好。冷轧堆工艺确实节能,其难点是堆卷处的温湿度必须严格控制,否则批与批之间的色重现性很难控制。
3.溶剂染色
3.1早在上世纪70年代,美国道化学公司的Dunn,Jr.开发了用三氯乙烯溶剂染涤纶的方法,不过氯氟碳氢溶剂均可适用,如三氯乙烷,氯甲烷,氟碳化合物F112,F1l3等。用分散染料溶剂染涤纶方法举例如下:
500克涤纶,用10克Resolin Brill Yellow TGL(2%o.w.f)溶于500ml过氢乙烯之中,总液量为 8.184升。升温至130℃保温60分钟,然后降至大气压.回收过氯乙烯。放在lg/L保险粉和lg/L氢氧化钠中,80℃洗20分钟,再放水加温至 80℃(液中含l%醋酸)洗10分钟,脱水后于105℃烘干(其中织物上有0.2%wt的过氯乙烯被带走)。
测染色物摩擦牢度,干为4级,湿为4+级
洗涤牢度和干洗牢度都是5级
耐晒牢度:可晒20小时。
3.2同时期意大利Monledison S.P.A.在毛织物上开发了三氯乙烯溶剂染色方法。
溶剂染色的关键因素是溶剂和水是两相不相溶的,通过乳化剂将西相乳化在一起,染色就均匀了。举例如下:
过氯乙烯3200份
乳化水10份
乳化水中含2份乳化剂,其中15.9%为吐温80(山梨醇单油酸酯加上20个环氧乙烷)和84.1%斯潘
80(山梨醇单油酸酯不接环氧乙烷)。染色时加人酸性黄39号1.77份→100份防缩羊毛纱。另外脂肪醇EO醚磷酸酯2份,十二烷基苯 磺酸1份,30分钟升温至100℃,保温60分钟寸移出→脱水→洗涤→烘干。染色具有很好的渗透性和吸尽率(98%)。
尼龙66纱染色例:100份尼龙66纱,于室温加1.67份酸性红57号,lO份水,乳化剂2份,3200份过氯乙烯,15分钟升温至100℃,保温45分钟→移出→水洗→烘干。吸尽率达99%。
目前问题是溶剂有毒禁止使用。要研发环境友好的溶剂如DPTB(即二丙二醇叔丁醚)等助剂。这对于干洗和溶翔染色都是当务之急。
4.羊毛低温染色趋势
羊毛低温染色研发至今已有20余年的历程,多年实践证明,低温染色80~90℃代替沸点染色不仅节约能源,而且对减少角元纤维损伤,尤其 是柔嫩的羊绒、兔毛、羊驼绒、羔羊毛等特种动物纤维的保持有重要意义。当今羊毛纤维染色保护剂羟甲基乙烯脲疑有甲醛释放、水解酰化蛋白对日益提高的摩擦牢 度有影响,在这种背景下,采取低温染色更不失为一种保护纤维的好方法。
以往为了低温的染色温控因素,限制了低温染色的推广,如今温度曲线的程序控制已很普遍,这一因素已不存在大问题。关键在于两点:作为角质纤维的主要膨化剂十八碳脂肪酰胺的乳化技术的研发需要进一步完善。
4.1作为乳化状态,现代染色需求的是微乳化状态,需要将十八碳脂肪酰胺的粒径通过微乳化技术细化到50--100nm,而不是以前的1.Oμm。膨化剂的微乳化可显著改进染色色牢度,减少浮色。
4.2另一点原来用壬基苯酚聚氯乙烯醚疑有毒(影响生育的一种环境类激素)待改为对环境更为友好的癸醇(ED)醚、异十三醇(EO)醚等作微乳化剂。
期待出现比BYLAN NT及Miralan Top更有效的低温染色助剂。
5.短蒸轧染工艺
5.1两种传统工艺的不足
包括棉、粘胶、麻及其与涤纶之混纺活性染料轧染,主要传统工艺如下
5.1.1轧一焙法
主要缺点是固色率低:得色牢度较差;色泽艳度不够好:脲素用量大。
5.1.2轧一烘一轧一蒸法
主要问题是用盐量大,环境污染大,染色成本高。
另外上述两种工艺对三原色混配的中间色,比如咖啡色、灰色、橄榄绿等色在头尾及色光控制上难度大。
针对这些问题,德国Monforts和Zeneca公司于1994年联合开发了湿短蒸染机及相关工艺。
5.2湿短蒸的优点
5.2.1该工艺流程短,汽蒸温度不太高而节约能源;
5.2.2减少用盐量、减轻废水处理压力;
5.2.3对难染的咖、灰、绿等色重现性及左中右、头尾色差控制得比传统工艺好;
5.2.4蒸箱含湿率始终保持在25-30%,织物渗透性好,固色率较高,色牢度好。
5.3湿短蒸轧染工艺关键因素
湿短蒸轧染工艺中有三个关键因素,PH值、蒸汽温度与时间。
5.3.1染液PH值
染液PH对染料的水解速度和直接性有很大影响,当PH增大时,活性染料对纤维素直接性也随之降低,同时染料的水解速度加快,高到某一值 时,直接性将急剧下降。例如活性艳红M-2BS在PH>10.5值时对纤维素直接性会急剧降低,加碱满足PH临界点的动态平衡。
5.3.2温度控制
生产中轧→焙工艺中,焙烘温度在160℃或以上;而轧→烘→轧→蒸工艺是在102℃饱和蒸汽中进行。湿短蒸为了兼顾染料的渗透性和固色率是在相对湿度25-30%,温度130℃进行汽蒸。
5.3.3汽蒸时间控制
实验证明,大量染料固色反应是在汽蒸时问超过2分钟,织物温度升高的阶段。一般汽蒸需3分钟。
5.3.4电解质的影响
由于湿短蒸工艺使染料分子有足够时问扩散,渗透,从而为纤维素提供染座及反应机遇,这样染色可省去促染用盐。冷轧堆染色在水、电、汽方面大约节约了45.6%,染色成本也有所下降。
6微胶囊染色
如果将染料包裹在微胶囊里,对纺织材料进行染色,染色时先将微胶囊里的染料通过抽真空溶解在纤维材料重量的5-20%的水中(传统工艺用水量是纤维材料的20-50倍),然后对纤维进行染色。这样水资源可大大节省。这一技术的关键在于微胶囊的制作。
6.1微胶囊所用材料
制作包裹染料用微胶囊材料都是热塑性的。如脲醛树脂、石腊基腊、酵母细胞、聚胺、聚氯之、烯偏聚氯乙烯、聚烯烃、聚酯、聚胺酯,聚胺基聚酯、聚丙烯酸、聚醋酸乙烯,聚苯乙烯或共聚物、聚脲等。
6.2微胶囊粒径在5μm至300nm的范围。
6.3染料微胶囊制作
酸性染料微胶囊的主要成分有聚合物,如本例中为阿拉伯树胶,水解动物明胶、甘露糖酵:溶剂聚氧乙烯醚(乳化剂T-60);去离子水,将上述各组分喷粉干燥,可得平均粒径为5.0№的微胶粒,其玻璃转化点Tg为45℃左右。
6.4在微胶囊中的各成分比例如下:
微胶囊成分 Wt%
酸性染料 68.0
阿拉伯树胶 6.5
微胶囊酸性染料制作举例如下:
水解动物明胶 13.75
甘露糖醇 5.0
二乙二醇单丁醚 1.25
乳化剂T-60 2.5
去离子水 3.0
上述各种染色工艺的研发,为各种羊毛及其混纺材料和散纤纱、毛条、机织、针织等材料形式的节水节能染色提供了多种选择,也为改善生态环境进行绿色生产创造了条件。
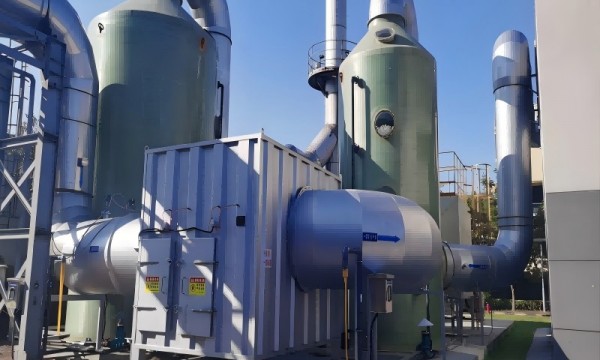
- 工业废气(臭气)净化处理
0评论2024-12-03
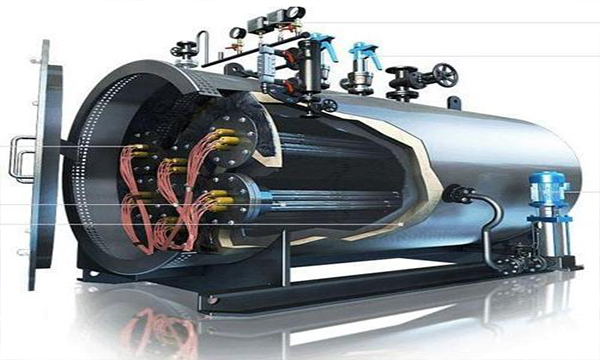
- 汽包锅炉和直流锅炉有何主要区别
0评论2024-07-30
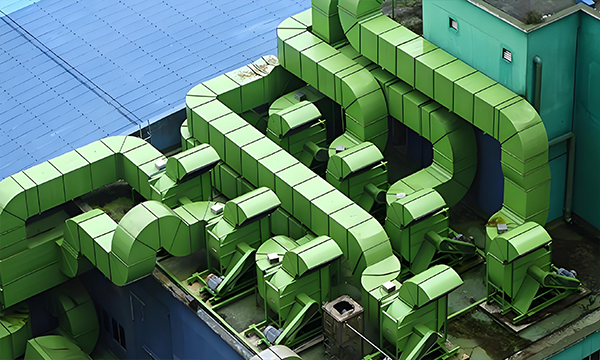
- 绿色暖通: 供热系统的节能挑战与解决方案
0评论2024-07-25
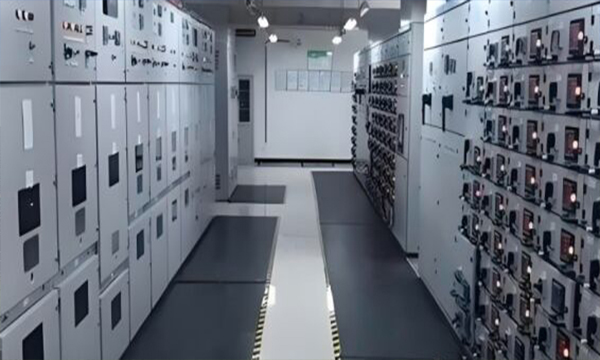
- 负荷计算与无功功率补偿全方位指南
0评论2024-07-19
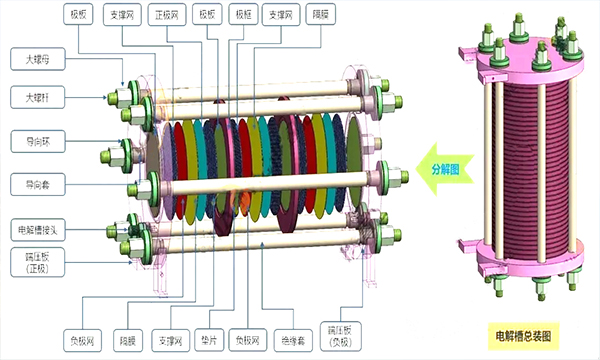
- 电解槽设备组件加工流程
0评论2024-07-19
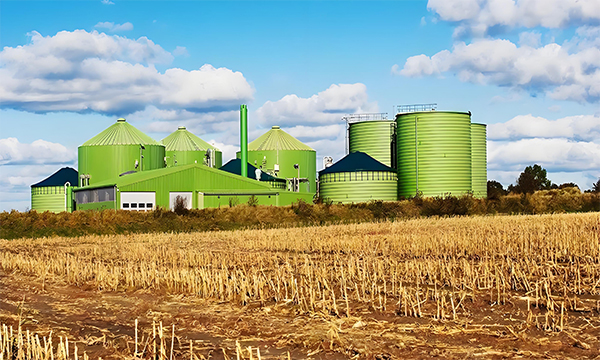
- 电厂生物质燃料碳减排技术创新与应用研究
0评论2024-06-30
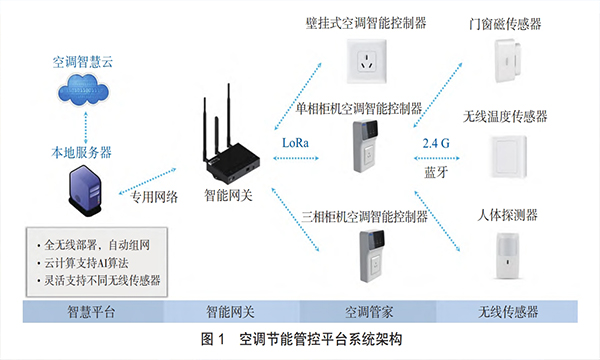
- 基于物联网和云计算技术的空调节能管控平台研究
0评论2024-06-28
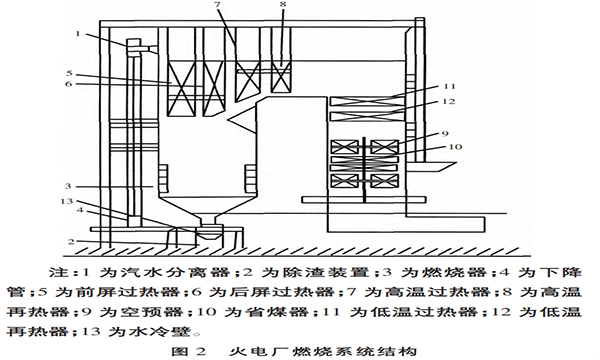
- 火电厂节能降耗技术分析及应用
0评论2024-06-26
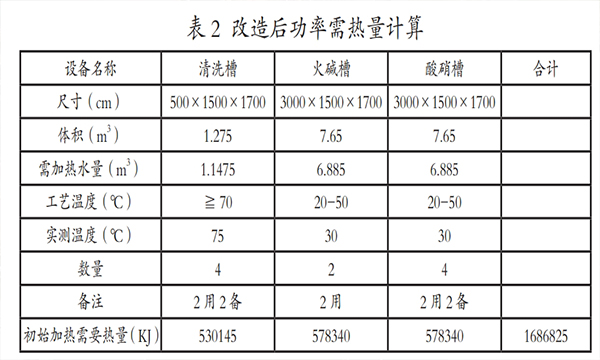
- 企业蒸汽加热系统节能降碳改造初探
0评论2024-06-25
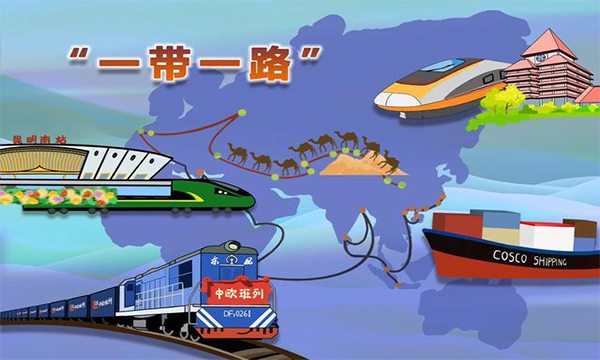
- “一带一路”背景下我国煤电节能环保改造技术装备走出去策略探索
0评论2024-06-25